In the field of packaging and printing, post-press processing is not only the last step in completing printed materials but also a crucial link in enhancing the texture of gift boxes and endowing them with artistic value. By carefully selecting and applying various post-press processes, gift boxes can be rejuvenated, increasing the added value of gifts and thus standing out in the fierce market competition. This article will share eight common post-press packaging techniques, allowing you to experience their unique charm.
In the printing industry, post-press processing is a vital link. It is not just a simple physical treatment of printed materials but also an important means of enhancing their value and ensuring quality. The purpose of post-press processing is to enable printed materials to achieve higher aesthetics, durability, and practicality through a series of elaborate technological operations, meeting the diverse needs of customers.
1. Lamination Process
Lamination, also known as "plasticizing" or "film laminating," is a technology that adheres a transparent plastic film to the surface of printed materials through heat pressing. It can not only enhance the gloss of printed materials, making their graphic colors more vivid, but also play roles in waterproofing, anti-fouling, and wear resistance. The lamination process is often used in the packaging of high-end gift boxes, adding a beautiful protective barrier to them.
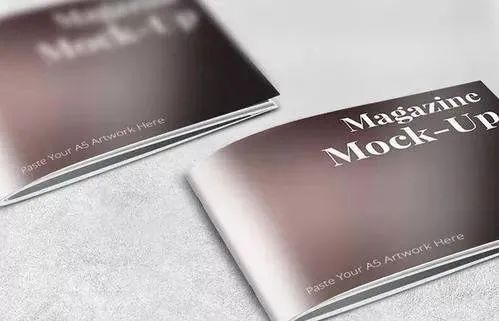
2. Hot Stamping Process
Hot stamping, commonly known as "gold stamping," is a processing technology that transfers hot stamping materials or plate patterns onto the substrate using a heated stamping head. It can create a strong metallic luster on gift boxes, endowing products with a noble and elegant texture. The hot stamping process is widely used in the decoration of various gift boxes and has become an important means of enhancing product grades.
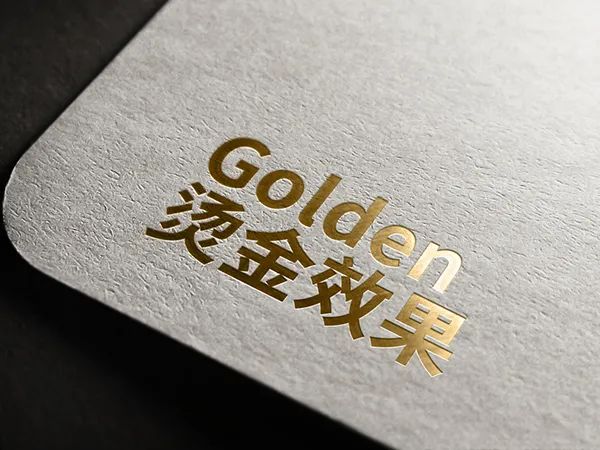
3. Glazing Process
Glazing is a process of coating a colorless and transparent coating on the surface of printed materials. After processes such as leveling, drying, calendering, and curing, a thin and uniform transparent and bright layer is formed. This process can enhance the smoothness of the printed material surface, protect the printed graphics and text, and simultaneously improve the overall texture of the gift box. The glazing process can be selected for full glazing or partial glazing according to requirements, achieving diverse decorative effects.
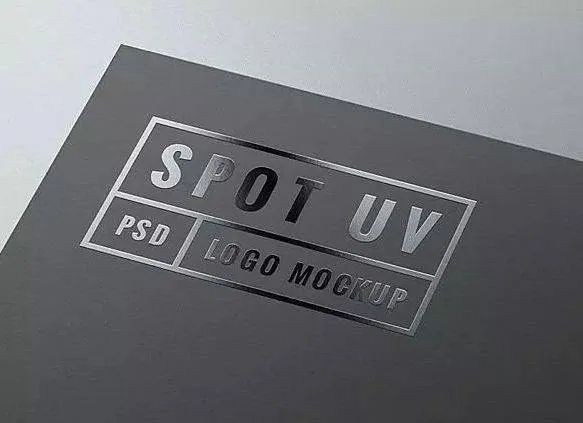
4. Embossing and Debossing Process
Embossing and debossing, also known as embossed printing, is a technology that conducts artistic processing on the surface of printed materials using embossing and debossing molds. Through the pressure of the molds, the base material of the printed material undergoes plastic deformation, forming graphic patterns and patterns with a relief effect. This process can significantly enhance the three-dimensional sense and artistic appeal of gift boxes, making them unique artworks.
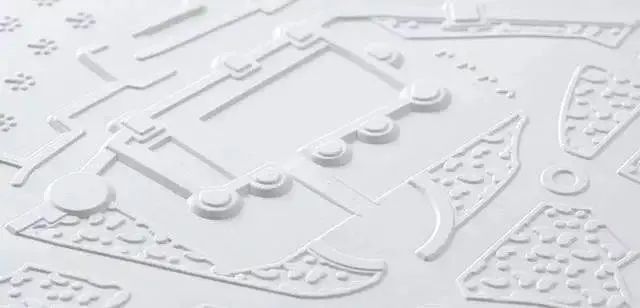
5. Die-Cutting and Scoring Process
Die-cutting and scoring is also known as die-cutting and forming, buttoning, etc. When packaging printed cartons need to be cut into a certain shape, it can be completed through the die-cutting and scoring process. Die-cutting is a process in which steel blades are arranged into a die (or a die is engraved from a steel plate), a frame, etc., and the paper is cut into a certain shape on a die-cutting machine. The hollowed-out part of the main display surface in the middle is obtained through the die-cutting process and becomes a personalized decoration in the entire packaging. Scoring is to use steel wires to press marks or leave grooves for bending on paper through stamping. The process of simultaneously performing die-cutting and scoring on a die-cutting machine is simply referred to as die pressing.
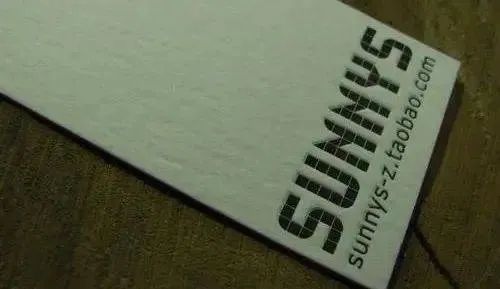
6. Partial UV Process
The partial UV process is a technology that locally coats UV varnish on the surface of printed materials through screen printing or flexographic printing. This process can enhance the dazzling effect of printed materials, making the glazed patterns appear more vivid, bright, and three-dimensional compared to the surrounding patterns. The partial UV process is often used for the decoration and embellishment of gift boxes, adding a touch of brightness to them.
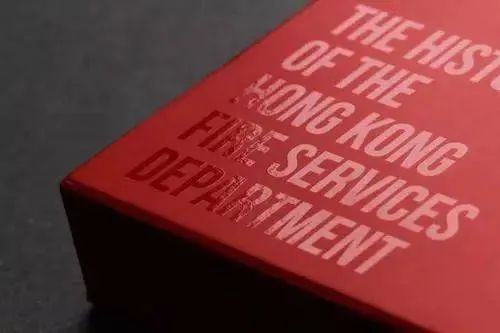
7. Reverse Frosted Process
The reverse frosted process is a post-press process achieved through multiple special base coat or varnish treatments, also known as the reverse glazing process. It can form a frosted texture coating on the surface of gift boxes, forming a sharp contrast with the conventional smooth surface. The reverse frosted process can endow gift boxes with a unique touch and visual effect, making them more artistic and personalized.

8. Frosted Snowflake Process
The frosted snowflake effect is achieved by screen-printing ink on substrates such as gold cardboard, silver cardboard, laser cardboard, and PVC. After being irradiated by ultraviolet light to wrinkle and UV-cured, a fine sand-like and delicate tactile effect is formed on the surface of the printed matter. Since it presents an effect like a thin layer of snow or ice on the surface of the printed matter, it is commonly known as "snowflake" (with larger patterns) or "frost point" (with smaller patterns) in the industry.
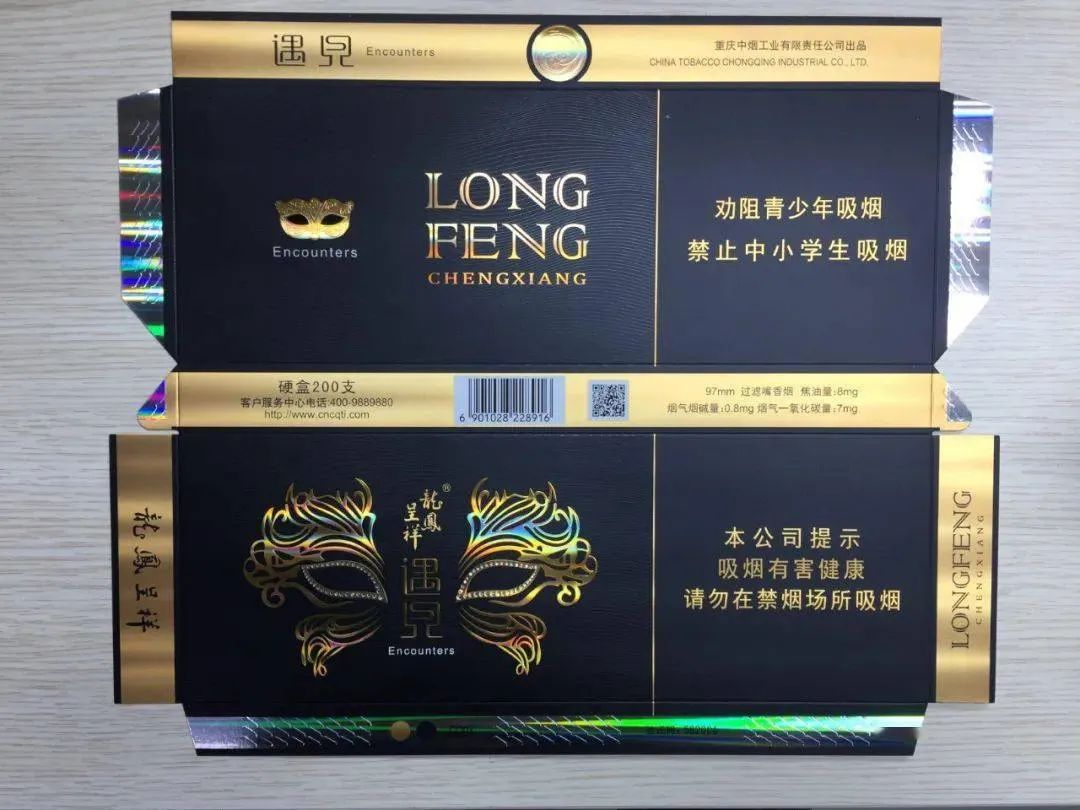
In conclusion, these eight post-press packaging processes each have their own characteristics and can add different artistic effects and textures to gift boxes. By flexibly applying these technologies, we can transform gift boxes into exquisite products, adding luster and charm to them.
Post time: Mar-03-2025