Pre-press, printing and post-press are the three major processes in modern printing technology. Each process directly affects the normal operation of the subsequent processes. Any printed product cannot do without the full cooperation of each process. A scientific and reasonable preliminary process design will have a multiplier effect on the progress of the later processes and plays an important role in ensuring product quality and improving production efficiency.
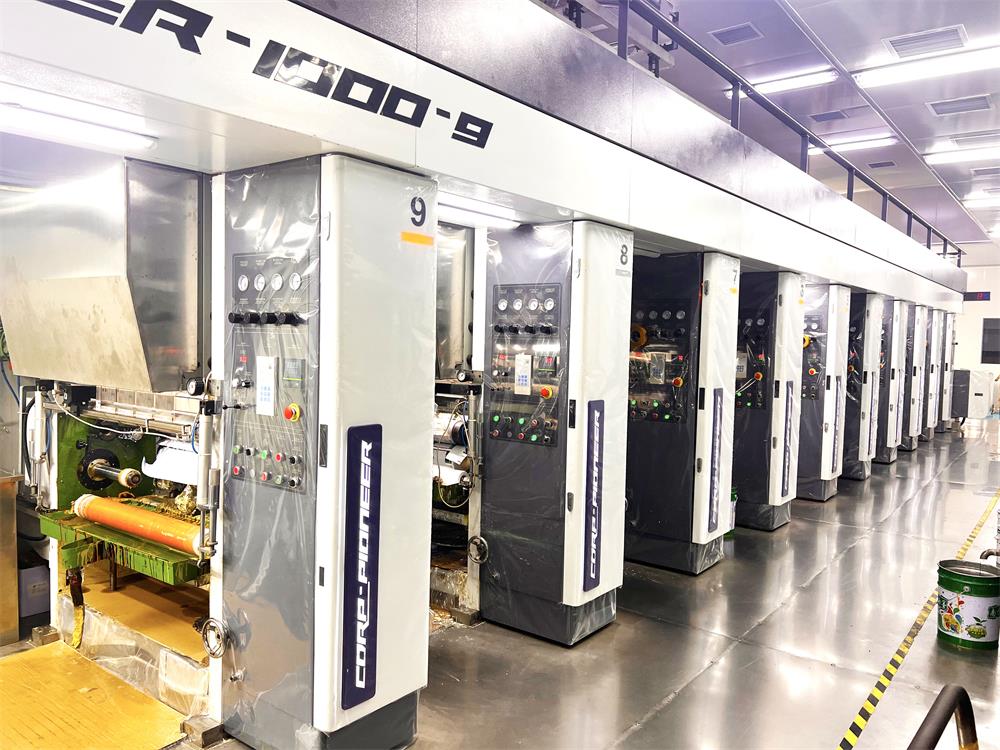
2. Text Printing: Texts generally follow the color of the layout, mostly in four colors, that is, texts appear in all four colors of CMYK. Especially for very small texts, it is difficult to register accurately, and it requires extremely high performance of the gripper teeth of the machine. This is also a relatively common problem. Therefore, before output, the pre-press designer must check whether the black texts in the publication file, especially small texts, only appear on the black plate and should not appear on the other three color plates. If they do, the quality of the printed finished product will be greatly reduced. When RGB graphics are converted to CMYK graphics, black texts will definitely become four-color black. Unless specifically specified, they must be processed. Therefore, it is recommended that texts be printed in spot colors.
3. Four-color Overprinting: The so-called four colors are cyan (C), magenta (M), yellow (Y), and black (K) inks. All colors can be mixed by these four inks to finally achieve color graphics. It is the most common and ordinary printing, and the printing effect on different substrates is different. For 4-color halftone and 3-color halftone, full-page colors should not be printed or printed in spot colors.
4. Superimposition of Several Color Dots. Of course, for a large flat screen like C = 50M = 50Y = 50K = 50 with more than 70% dots. Specifically, dark brown, coffee color, dark green (flat screen, containing 70% blue), dark blue, and violet-blue colors are difficult to print due to color differences and are difficult to balance on the printing machine. Therefore, spot color plates need to be made.
5. Gray Balance: It refers to the generation of neutral gray on the printed matter by the yellow, magenta, and cyan color plates according to different dot area ratio. According to theoretical and production practice experience, the most difficult color to control in printed matter is gray balance. Gray balance is to obtain different brightness achromatic colors (white, light gray, gray, dark gray, black), that is, visually neutral gray colors, by superimposing and combining the three primary color plates of yellow, magenta, and cyan from light to deep in a certain dot ratio under certain printing suitability. Many factors affect it, such as the ink amount used in printing, paper, full-page concentration, dot area, overprinting, and screen ruling, all of which have a complex impact on gray balance. This is the most challenging test for the registration accuracy of the machine and the skills of operators.
6. Production Method of Screen Printing Plate Making in Color Register Printing in Plate Making Factory - Silk Screen Paper Cutout Plate Making: Copy the designed drawing with tracing paper, and then copy the traced drawing onto silk screen paper with copy paper for each color. Copy several silk screen papers for several colors. Before copying on the silk screen, mark " + " calibration marks at the top and bottom of the blank area of the drawing on the tracing paper. Then, use the same method to copy the upper and lower " + " calibration marks on the silk screen paper of the same size, so that when making the color register silk screen plate, a well-matched color picture can be accurately registered.
The printing process is essentially the transfer process of ink. After being output from the ink transfer roller, the ink is transferred to the inking roller through the ink distributing roller, then to the printing plate, then to the blanket, and finally to the substrate to complete the printing process. Ink with good transferability can evenly distribute the ink amount when the ink film is separated on the ink rollers of the printing machine. After multiple transfers, it can increase the uniformity of the ink layer, ink color concentration, and fullness on the surface of the printing plate. When the ink transferability is poor, the ink amount transferred to the printing plate or blanket is insufficient, which is likely to cause the graphic and text base of the printed matter to be exposed, resulting in the phenomenon of plate wear, or cause uneven ink color between the ink distributing rollers and excessive ink accumulation, resulting in ink color unevenness, flying ink, and drying and film formation on the surface of the ink rollers.
In short, a qualified printed product must meet the following requirements: 1. Precise registration; 2. Uniform ink color; 3. Full dots; 4. Water-ink balance; 5. The printed product has no printing defects such as set-off, scratches, petal-shaped patterns, and paste-up; 6. Strictly faithful to the original manuscript. Printing enterprises must pursue high-quality printed products to adapt to the increasingly improved aesthetic concepts of people.
Post time: Dec-13-2024