The color and quality of offset printing rely on the ink-water balance. Here, we particularly emphasize the stability of the "function" of the entire water and ink supply system. The following are six aspects that require the most attention and control:
Stable Rotation Amplitude of Ink Tank Roll and Ink Beating Function
Normal Function of Ink Key Opening/Zero Setting/Remote Control
Normal and Stable Contact Function of Water and Ink Rolls with the Plate
Correct Composition and Proportion of Fountain Solution and Alcohol
Normal and Stable Refrigeration/Circulation/Monitoring/Replenishment Functions of Fountain Solution
Uniform and Stable Diameter and Pressure of Ink and Water Rolls
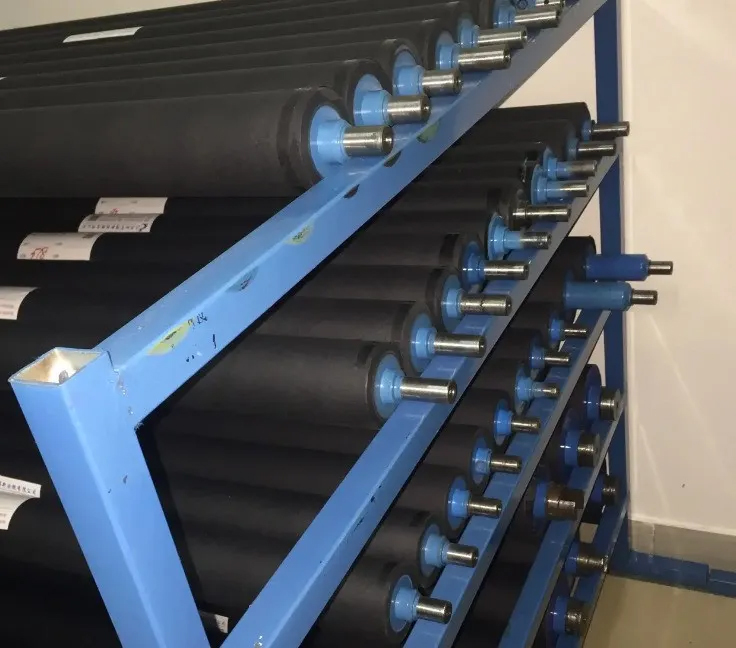
1. Stable Rotation Amplitude of Ink Tank Roll and Ink Beating Function
The principle of ink supply in an offset printing press is to control the ink layer thickness in each area through ink keys and then control the rotation amplitude of the ink transfer roller and ink tank roller in contact to control the ink output of the entire printing format. Therefore, the stability of the remote control opening and closing function of the ink keys and the rotation speed/amplitude function of the ink tank roller determines the stability of the ink output and color of the unit. In the long term, the main factors that are more likely to cause instability are the wear of the ink key opening, followed by the unstable rotation speed of the ink tank roller and the pressure of the ink transfer roller.
2. Normal Function of Ink Key Opening/Zero Setting/Remote Control
Regarding the ink key function, we should pay special attention to whether the remote control and ink key opening are normal and stable. More specifically, if the remote control function fails, it will be very difficult for the press operator to control the ink color correctly and in a timely manner. On the console, if we set the ink key opening to 4 grids, but the actual opening of each ink key is neither uniform nor standard; when setting the ink keys to zero, some ink key positions cannot return to the zero position; similarly, the press operator cannot control the printing color effectively and accurately. In this regard, what we should be most concerned about is whether the same ink key setting can be stably reproduced each time, which is a very important basis for stable printing color.
3. Normal and Stable Contact Function of Water and Ink Rolls with the Plate
Different brands of printing presses have different programmed functions for the lower water and ink rolls (contact with the plate). Some printing presses will rinse the plate with the maximum amount of water after the lower water roll, and after several rotations, arrange for the ink rolls to automatically contact the plate. Some printing presses can also be set so that after the printing pressure is released, the water roll remains on the plate for several rotations before automatically leaving the plate. If these functions fail, they will to some extent affect the printing color and quality.
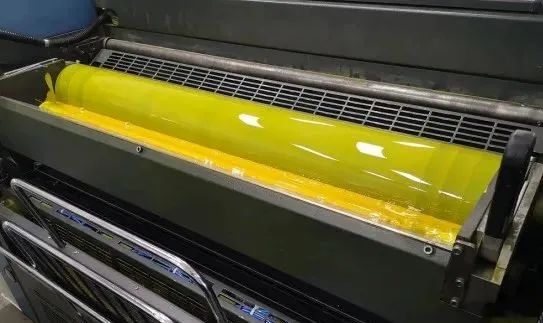
4. Correct Composition and Proportion of Fountain Solution and Alcohol
The fountain solution usually consists of fountain concentrate, alcohol, and water. We must pay attention to the stability of the physical properties of these three materials and whether the proportion is correct. Whether the purity of the incoming alcohol/fountain concentrate is diluted, whether the quality of tap water is too hard with excessive calcium content, etc., will directly affect the stability of printing color.
5. Normal and Stable Refrigeration/Circulation/Monitoring/Replenishment Functions of Fountain Solution
The refrigeration function of the fountain solution is very important in printing. It not only affects the amount of water on the plate but also involves the cooling of water rolls (water rolls also generate frictional heat) and the heat absorption of ink rolls. Press operators are well aware that once the refrigeration fails, the ink-water balance in printing will change immediately. Even if the water amount is increased to 100%, the plate will still get dirty.
The circulation function of the fountain solution mainly provides cooling water continuously, recovers heated and polluted water, and maintains the temperature stability of the water and ink roll system. Of course, it has a direct impact on the stability of printing color.
There are four indicators of the fountain solution that must be accurately monitored, namely water temperature, alcohol concentration, pH value, and conductivity. If any deviation is found, it must be corrected in a timely manner. If the water temperature is high, the refrigeration should be automatically started. If the alcohol evaporates and the concentration is insufficient, the addition should be started immediately. When the fountain solution in the tank is used up, the fountain concentrate and tap water must be replenished immediately.
The monitoring and replenishment functions are equally important because any deviation will immediately affect the stability of the printing color.
6. Uniform and Stable Diameter and Pressure of Ink and Water Rolls
The ink and water rolls of the printing press will gradually wear and become smaller with use. At the same time, due to the action of the ink distributor rollers, all rubber rollers will have a wear pattern with smaller diameters at both ends and a larger diameter in the middle (UV rollers will have larger diameters at both ends and a smaller diameter in the middle). A smaller diameter directly affects the ink storage capacity; uneven ink/water rolls or uneven pressure between rolls directly affects the uniformity of ink and water supply. In the long term, these are factors that cause changes and instability in the condition of the printing press.
Post time: Dec-13-2024