The laminating process and the glazing process both belong to the category of post-printing surface finishing processing of printed matter. The functions of the two are very similar, and both can play a certain role in decorating and protecting the surface of the printed matter, but there are differences between the two:
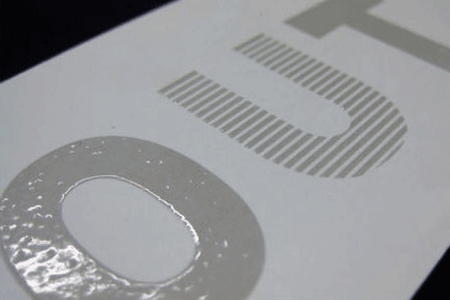
Surface finishing
Surface finishing is to perform appropriate processing on the surface of the printed matter to improve the light resistance, water resistance, heat resistance, folding resistance, wear resistance and chemical resistance of the printed matter; increase the gloss and artistic sense of the printed matter; and protect the printed matter. And the function of beautifying printed matter and increasing the value of printed matter. Common surface modification methods for printed matter include glazing, lamination, foiling, die-cutting, creasing or other processing.
01 meaning
Lamination is a post-printing process in which a plastic film coated with adhesive is covered on the surface of a printed matter. After heating and pressure treatment, the printed matter and the plastic film are closely combined to become a paper-plastic integrated product. The laminating process belongs to the paper-plastic composite process in the composite process and is a dry composite.
Glazing is a process in which a layer of colorless transparent paint is applied (or sprayed or printed) on the surface of a printed matter. After leveling and drying (calendering), a thin and even transparent bright layer is formed on the surface of the printed matter. The process is coating (commonly known as The process of applying varnish (including film-forming resin, solvent and additives) to the surface of printed matter for leveling and drying.
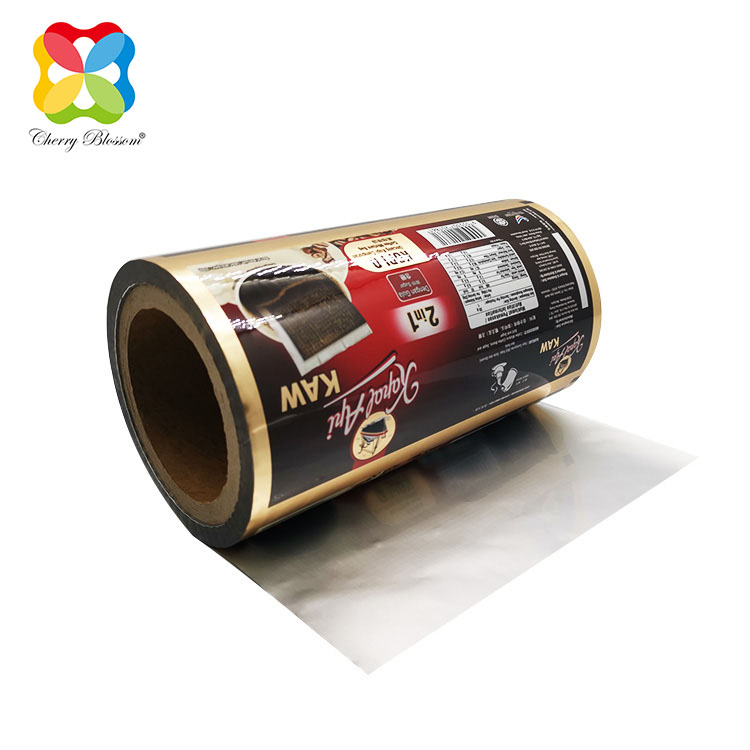
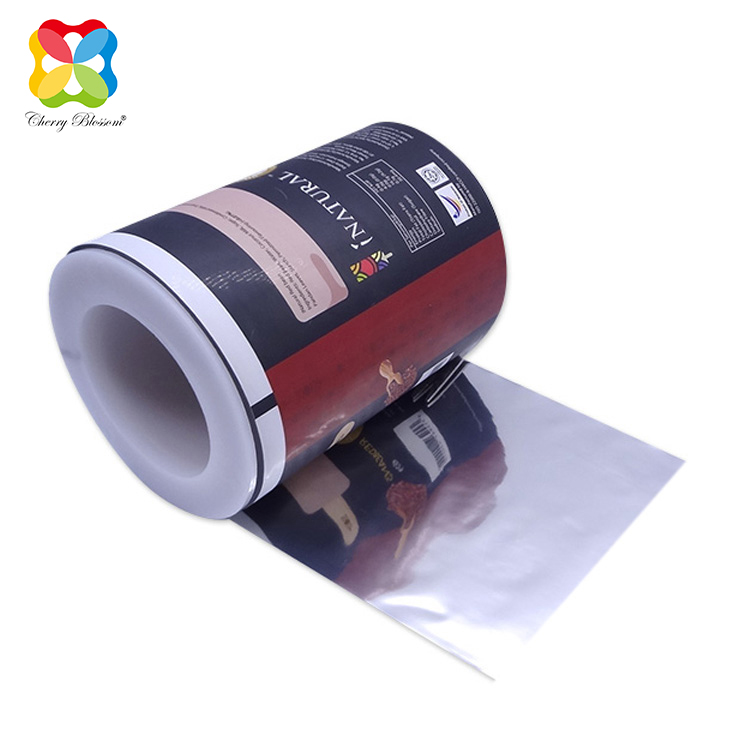
02 Function and meaning
After the surface of the printed matter is covered with a layer of plastic film (coating) or coated with a layer of glazing paint (glazing), the printed matter can be made to have the functions of friction resistance, moisture-proof, waterproof and anti-fouling, etc., which not only protects the printed matter, but also protects the printed matter. Extending its service life, it also improves the brightness of the surface of the printed matter, enhances its ornamental value, makes the printed graphics and text bright in color, and has a strong visual effect, thus improving the quality of the product and increasing the added value. For example, book cover lamination, surface glazing of cosmetic packaging boxes, etc.
Therefore, laminating and glazing are one of the main processing technologies for post-printing surface finishing of printed matter. They can not only "brighten" the surface of the printed matter and attract consumers' attention, but also protect the printed matter and improve its performance. They are now widely used. It is suitable for surface decoration of books, periodicals, picture albums, various documents, advertising brochures and surface decoration of various paper packaging products.
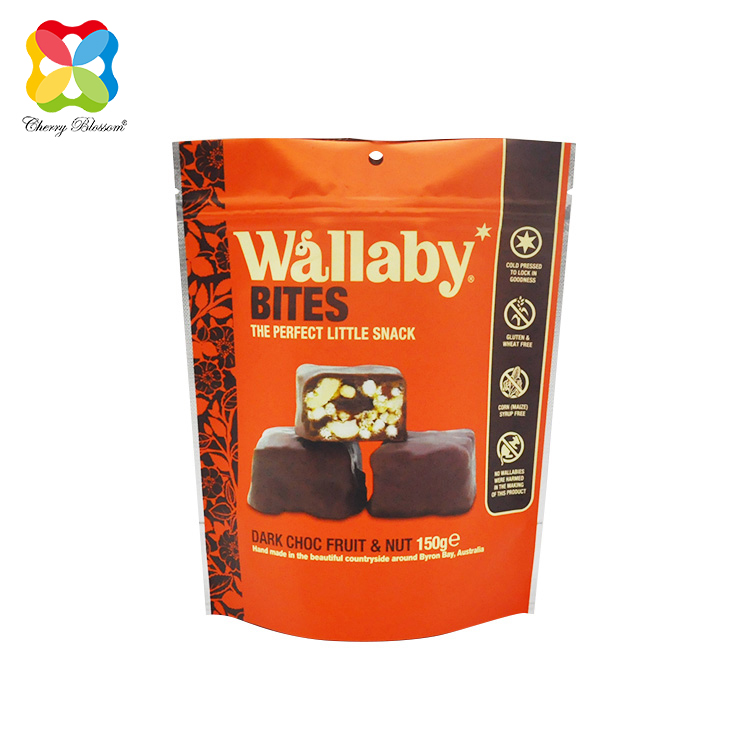
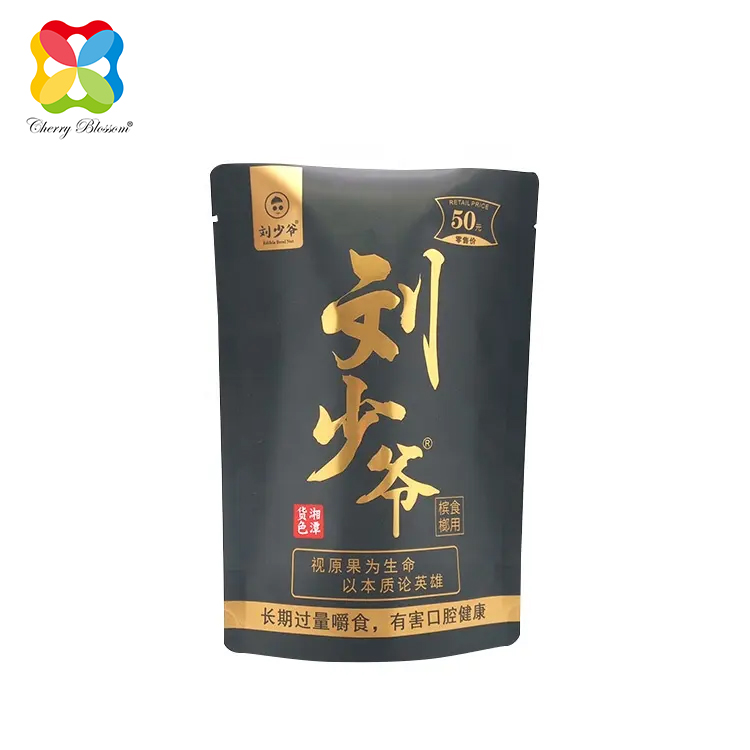
03 The process is different
Film coating process The film coating process can be divided into instant coating film technology and pre-coating film technology according to the different raw materials and equipment used.
1) The coating film process first uses a roller coating device to evenly coat the adhesive on the surface of the plastic film. After passing through the drying device, the solvent in the adhesive is evaporated, and then the printed matter is pulled to the hot pressing lamination device. On the machine, the plastic film and the printed matter are pressed together to complete the lamination and rewinding, and then are stored for shaping and slitting. This method is currently commonly used in China. From the perspective of the adhesive material used in the coating film, it can be divided into solvent-based adhesive film and water-based adhesive film.
2) Pre-coating film The pre-coating film process is for professional manufacturers to pre-quantitatively and evenly apply adhesives on plastic films, dry, rewind, and package them into products for sale, and then processing companies apply adhesive-free coating on them. Hot pressing is performed on the laminating equipment of the device to complete the laminating process of the printed matter. The pre-coating film process greatly simplifies the coating process because the coating equipment does not require an adhesive heating and drying system, and is very convenient to operate. At the same time, there is no solvent volatilization and no environmental pollution, which improves the working environment; more importantly, it The occurrence of coating quality failures such as bubbles and delamination is completely avoided. The transparency of the coated products is extremely high. Compared with the conventional coating process, it has broader application prospects.
1) Solvent-based glazing Solvent-based glazing refers to a glazing process that uses benzene, esters and alcohols as solvents and thermoplastic resin as film-forming resin. During the glazing process, the solvent evaporates and the resin polymerizes or Cross-linking reaction forms a film. It is characterized by small equipment investment and low cost, but the solvent volatilization and residue on the printed matter will cause environmental pollution and be harmful to the human body.
2) Water-based glazing Water-based glazing is a glazing method that uses water-soluble resin or different types of water-dispersed resins as film-forming substances. Water-based glazing paint uses water as the solvent, and there is no organic solvent volatile matter during the coating and drying process. The characteristic is that the glazing process has no irritating smell, no pollution to the environment, and is harmless to the human body. It is widely used in the packaging of tobacco, medicine, food, cosmetics and other commodities.
3) UV glazing UV glazing is ultraviolet radiation dry glazing. It uses ultraviolet rays to irradiate the glazing oil to instantly trigger a photochemical reaction of the glazing oil to form a bright coating with a network chemical structure on the surface of the printed matter. The glazing curing process is the same as the drying process of UV ink. It is characterized by good gloss, strong heat resistance and wear resistance, fast drying, safety and environmental protection. It has broad market development prospects. Like water-based glazing, it is mostly used in medicine, food, etc. Product packaging in the field.
Post time: Dec-13-2023